sectores
Automotive industry
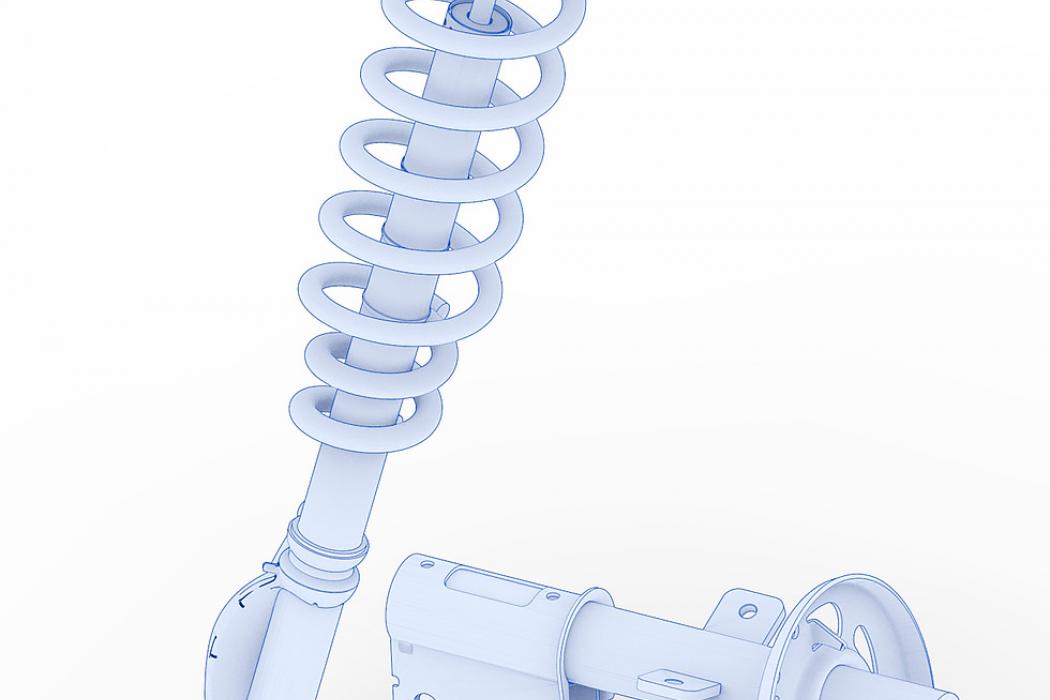
LAUNIK is a leading supplier of automated solutions for the production of shock absorbers, having worked with the sector's leading manufacturers for decades.
LAUNIK is a leading supplier of automated solutions for the production of shock absorbers, having worked with the sector's leading manufacturers for decades.
Sectors
Hinges / Retainers
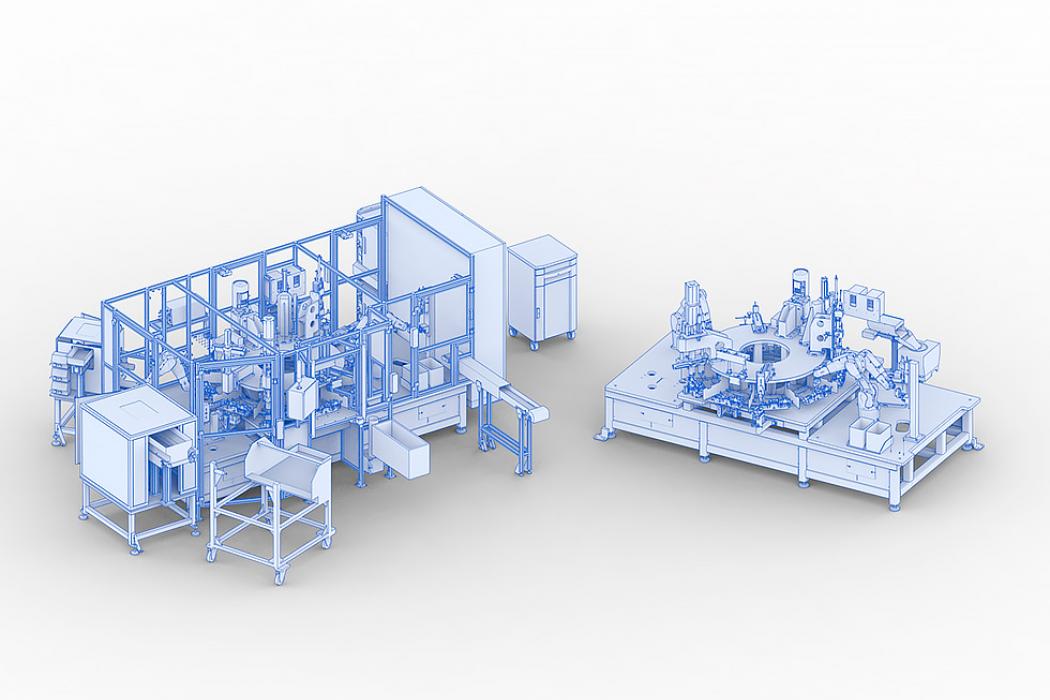
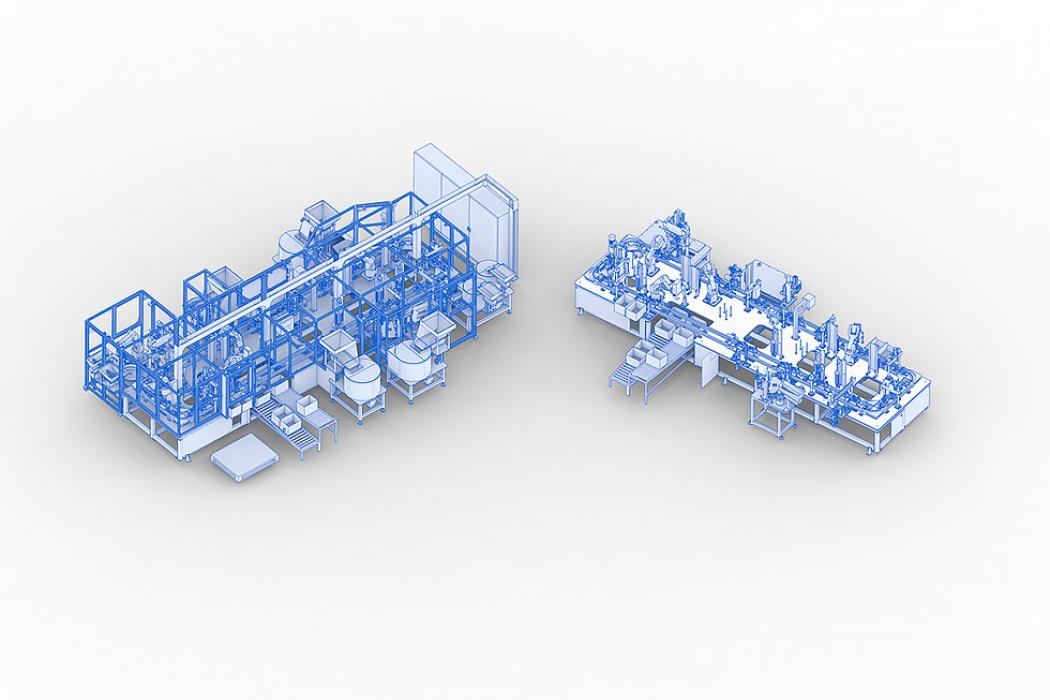
Rotary transfer machine for assembly
LAU-NIK is a supplier of hinge and retainer assembly cells that meet the highest cycle time and OEE requirements
Palletised assembly lines
When the assembly operations or the customer so require, all the processes are integrated automatically on palletised lines.
Sectors
Steering / Chassis
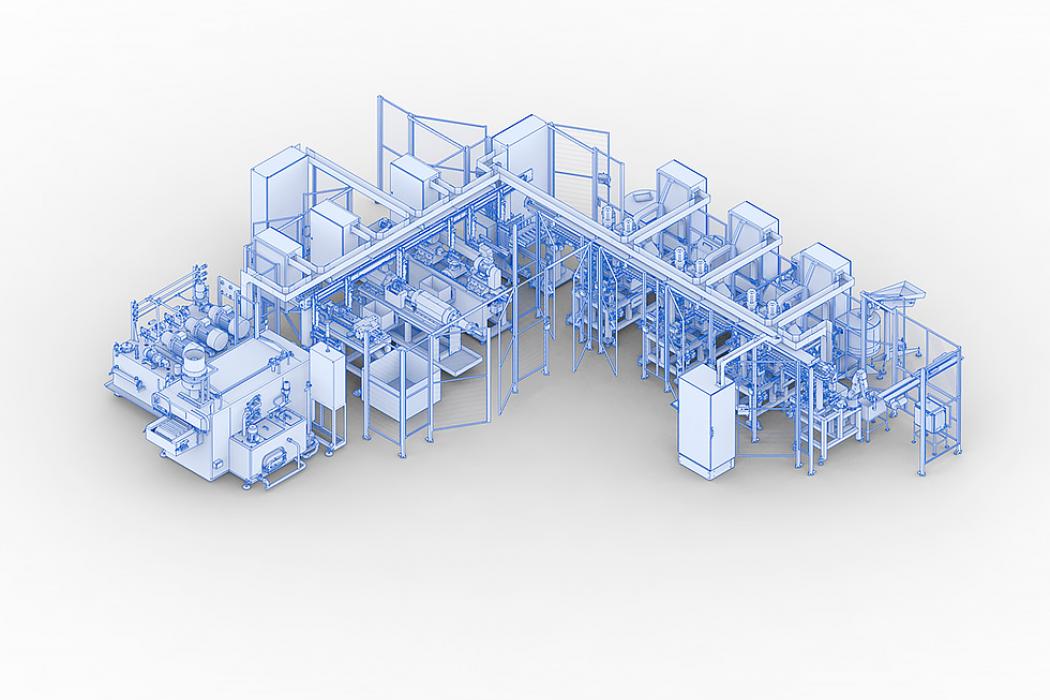
Steering column / airbag tube manufacturing lines
In partnership with one of the sectors’ TIER 1 manufacturers, LAU-NIK supplies steering column tube forming, punching and welding machines. Precision, finish and mechanical performance are essential in a vehicle safety system like the steering system.
Tube and chassis part manufacturing machines
Both comprehensively on the assembly line and individually, LAU-NIK provides all automatic solutions involved in the manufacture of the tube and the structural parts, using technologies like pressing, roll closing, welding, measuring, vision and marking.